ADDED VALUE
Our added value propositions are what set C&W apart:
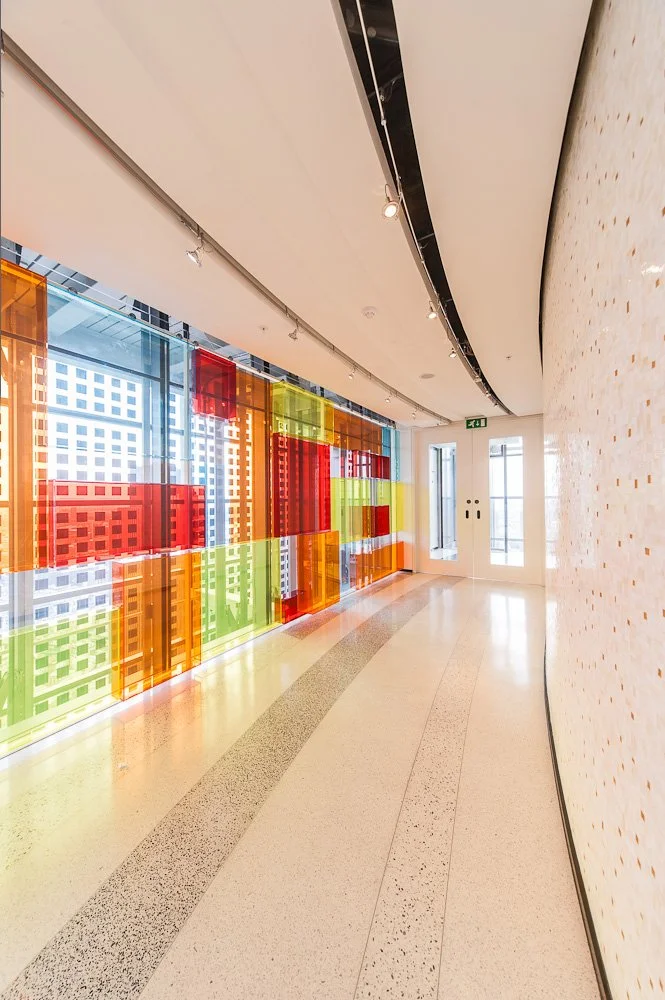
DIRECTOR INVOLVEMENT
Each project, no matter how big or small, will be allocated to one of the Owners/Directors of the business. This ensures that each project will have at least a Project Director, Project Manager and Owner/Director allocated.
BUSINESS AS USUAL STATUS
Maintaining a business as usual status during the refurbishment process is essential to any successful business.
DESIGN WORKSHOPS
Our preferred method for ensuring comprehensive design co-ordination is the implementation of multi-trade design workshops during the early stages of the project. Whilst not essential we encourage the involvement of the design team in this process to assist in the realisation of their design proposals and improve the overall approval / comment process.
BENCHMARKING
Establishing and agreeing from the outset a quality plan which would set out the project specific elements that we believe will require mock up and benchmarking to ensure a ‘right first time’ approach to the works.
3RD PARTY COMMISSIONING
It is company policy that 3rd party validation and commissioning is carried out on all our projects to offer absolute transparency and protect the interests of all parties involved in any project. Early establishment of commissioning strategy and timely provision of integrated systems test.
SUPPLY CHAIN QUALITY CONTROL
C&W have a stringent prequalification process to maintain a high quality of workmanship right from the beginning. Performance is regularly reviewed, and our supply chain continually monitored and improved.
CCS
Each project with suitable criteria is registered with CCS. Each project manager at C&W is incentivised to achieve a score of 40+ on each project. We also have a ‘CCS Champion’ who champions the cause, hosts workshops with our operations staff, sets targets on individual projects, tracks ‘good practice’ and communicates with site teams and subcontractors alike. We aim to achieve at least 35 out of 50 on all of our jobs and are aware of the need to score at least 7 in all 5 sections.
QUALITY & CONTROL PROCEDURES
Our process for achieving snag free status at PC is based upon a philosophy of snagging from Day 1, not at the end of the project.
PLANNING FOR QUALITY
In preparing our ‘Quality Plan’ we will set out those elements of the works that require factory inspections, mock-ups, benchmarking or testing and will make all necessary arrangements and allowances within our bid.